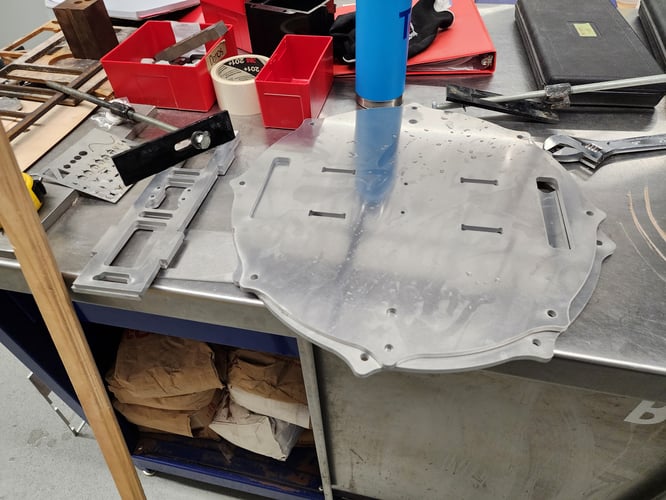
RoboGames is only a month away, and we've been super busy converting Torment Nexus from an idea to a lean mean spinning machine.
We have been super fortunate to raise over $10,000 in cash and in-kind services from extremely generous sponsors, without which Torment Nexus would not exist. Thank you to Elko Engineering Garage, Promac Industries, 5i Research, Chase Operator Training, and Tilted Pixel for supporting the project!
Here are just a few of the things we've accomplished in the last month:
CAD Design
A tremendous amount of work went into the CAD design, making it possible to visualize and ultimately manufacture the complex interlocking parts that form Torment Nexus.
The robot consists of a large outer ring with teeth designed directly into it and cut from a single billet of aluminum. The insides are designed as assemblies that fit neatly into the chassis and are kept in place and sandwiched by the top and bottom baseplates.
Custom designed AR500 teeth are mounted over top of the aluminum teeth, providing the necessary hardness to withstand the ridiculous energy that we expect the bot to hit with!
Cutting the "Ring of Doom" Aluminum Chassis
The design includes many parts that require waterjet, CNC machining and 3d printing to manufacture. But none are quite as challenging as the giant ring of doom that forms the outer part of the chassis.
To make the ring possible we had to source the 18"x18" aluminum billets, which included a road trip to get them from Calgary to Edmonton. The billets then had to be cut on a waterjet capable of cutting through the 3.5" thickness (4 hours of cutting per billet!), thicknessed down to size on a lathe, and they are currently awaiting the tooling needing to machine the inner groove and other details.
We were extremely fortunate to have access to the equipment of Elko Engineering Garage and the tremendous expertise of Nick to make this possible.
The waterjet cut through the 3.5" aluminum and gave us the basic shape. Finer details will need to be machined in.
Turning the wheel of doom to final thickness!
Custom Wheels and Shafts
The tires of a melty brain must be:
- Soft enough to provide enough traction to spin rapidly on a steel floor and not slip.
- Durable enough to not send tire material flying in every direction when subjected to the extreme G forces caused by rotating thousands of times per minute.
To give us the best chance of meeting these criteria we opted to pour our own urethane tired molded directly to custom wheel hubs. The hubs are designed to give the urethane a lot of places to stick.
The hubs are then mounted on custom shafts designed to keep the wheels on tight!
Will our design hold up? We will find out soon!
Thank you to Wes and the Promac Industries team for creating the beautiful wheel hubs, as well as the custom shafts that fit into them.
Electronics, Code, and Custom Circuit Boards
The "brain" part of "melty brain" hints at what makes this style of combat robot so unique and so challenging.
Most combat robots are essentially remote control cars (with weapons attached). If you press forward on the radio, a command is sent directly from the receiver to the robot's speed controllers telling both wheel motors to spin. If you turn left or right, the wheels turn in opposite directions to cause the robot to turn.
Melty locomotion is a bit more...complicated. If the wheels of Torment Nexus are used to spin the robot up to several thousand RPM, then how does it move around? That's where the "brain" comes, specifically a microcontroller that translates the driver's desire to in a particular direction into precisely timed adjustments to the speed of each wheel, causing the bot to (hopefully) move in that direction while continuing to spin.
This type of control system hinges on having the right sensors in place to detect which direction the robot is "facing" at ridiculous sample rates, and quickly and accurately translating this into the necessary wheel adjustments. A lot has to go right, or the bot will simply hockey puck around the arena or (worst) just sit there spinning in one spot until it gets counted out.
The electronics for this brain have been designed and the custom circuit board will be arriving any day now.
BOM and Supply Chain Management
Keeping track of what parts are actually needed for a combat robot, and finding ways to acquire them in Canada (without bankrupting the team), is its own challenge.
From pallets with aluminum billets strapped to them to tiny but expensive packages of electronics, we have worked very hard to ensure every motor, bearing, fastener, and connector matches the specs we need, is accurately documented, and most importantly, arrives to us in time (with some longer-lead time or hard-to-source parts this is critical!).
Gotta Have Merch!
If you're going to build a combat robot, you gotta have merch too! Torment Nexus officially has a logo, and will be placing a hat and shirt order shortly (contact matt.inglot@gmail.com if you are interested in either!).
Find us at RoboGames and we may have something else as well...
The Road From Here to RoboGames
It's been an incredibly productive month, but there's lots to go. Over the next month we will be:
- Assembling all the things.
- Soldering all the things.
- Writing and testing the code needed to operate the melty.
- Building the necessary setup to safely test a 3d printed version of the bot (Plastic Nexus)
- Getting the robot packed up and ready for RoboGames.
That's the short list anyway. Wish us luck!